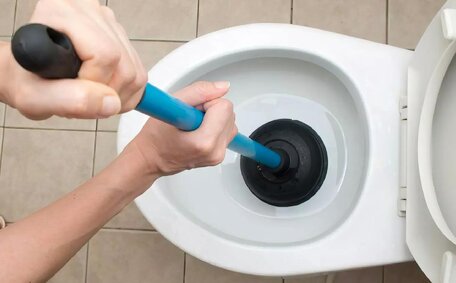
How to Prevent Household Blocked Drains
Blocked drains can be prevented by using drain strainers, avoiding pouring oils down drains, clearing hair from drains, and more tips from Seven Hills Plumbing.
Read MorePressure testing gas lines is a critical safety procedure required for all new gas line installations and existing gas systems. At Seven Hills Plumbing, we specialise in professionally pressure testing gas lines to check for leaks and ensure your gas system is safe.
The purpose of gas line pressure testing is to verify the integrity of the piping system and identify any leaks before gas is supplied. High-pressure gas leaking from fittings, joints or pipes can lead to dangerous explosions and carbon monoxide poisoning. That’s why strict standards exist for acceptable pressure levels during testing.
There are two main methods of pressure testing a gas line - hydraulic testing and pneumatic testing. Hydraulic testing involves filling the gas gas pipe with a water column or an inert fluid and pressurising it. We use advanced equipment to pressure test and monitor it during the testing of natural gas line components.
Pneumatic testing introduces compressed air to emulate the natural gas pressure within the system.
At Seven Hills Plumbing, our commitment to gas safety and the protection of your family drives us to excel. Please reach out for detailed insights into our meticulous gas line pressure testing process that complies fully with current regulations and standards.
That’s emissions from any gas leaks, applicable to both new and existing systems.
Pressure testing verifies that the gas line can withstand the maximum operating pressure without any leaks. It involves pressurising the line with air or an inert gas and monitoring pressure gauges. If the pressure drops during the test, it indicates a leak that must be repaired before gas can be supplied.
Following any repairs, extensions, or changes to the gas system, a re-test is required to ensure pressure stability. We recommend annual checks for both commercial and residential systems to identify and promptly fix any leaks, which can cause a dangerous build-up of gas.
Regular pressure testing by gas fitters helps prevent disasters, ensuring safety and efficient gas appliance operation—avoid shortcuts and opt for comprehensive testing to ensure gas line integrity.
Performing pressure tests on gas lines is vital for protecting the safety of your home or business.
Mandated by law, thorough pressure testing avoids the risk of explosions and carbon monoxide emissions from any gas leaks, applicable to both new and existing systems.
Pressure testing typically occurs before connecting the gas line to the supply, with precise test pressures applied based on gas type and pipe material, highlighting the emphasis on safety.
There are two primary methods used for pressure testing gas lines - hydraulic testing and pneumatic testing.
Hydraulic testing involves filling the gas line with a liquid, usually water, and pressurising it. This test method is considered extremely safe as water is incompressible, so if a leak occurs, water will escape slowly rather than gas exploding out.
Pneumatic testing employs compressed air or inert gases, such as nitrogen, to pressurise the line and is typical for low and medium-pressure lines, usually those under 200 psi.
Pneumatic testing is faster and cheaper than hydraulic testing. However, compressed air can accelerate leaks, so extra safety precautions are necessary. The line must be thoroughly vented after testing to remove all gas volume.
Our proficient gas technicians possess extensive experience conducting tests on systems using natural gas or propane, ensuring the most suitable method is applied for compliance with industry norms.
There are two primary methods used for pressure testing gas lines - hydraulic testing and pneumatic testing.
Hydraulic testing involves filling the gas line with a liquid, usually water, and pressurising it.
Hydraulic and pneumatic testing, each with distinctive benefits, stand as the primary methodologies for pressure testing gas lines.
Pneumatic testing uses compressed air or inert gas to pressurise the line. It is faster and more economical than hydraulic testing, but extra safety precautions are necessary. Pneumatic testing is suitable for low pressure and medium pressure gas lines under 200 psi.
At Seven Hills Plumbing, Our gas fitter professionals ensure your system can withstand up to the specified test pressures using industry best practises for hydraulic or pneumatic testing. Both test methods allow us to thoroughly check your gas system for leaks before commissioning.
The standards require that for consumer piping, a pressure test should show no more than a 3.5 kPa drop within a 15-minute window, while high-pressure pipeline criteria differ.
By adhering to these gas standards, we ensure all pressure tests on new and existing gas service lines meet the necessary safety levels. This gives clients confidence their gas system is compliant and reduces risks.
Meticulous preparation is key to conducting a gas line pressure test safely and in compliance with regulatory standards. Here are the essential steps gas fitters undertake in preparation for the test:
At Seven Hills Plumbing, we take care to ensure every gas line is thoroughly prepared before pressure testing. This enables us to complete testing efficiently while adhering to Australian standards and mitigating safety risks.
Gas line pressure testing should only be conducted by qualified professionals ensuring the correct amount gas pressure is applied following all applicable safety procedures. At Seven Hills Plumbing, we execute tests to Australian Standards to verify your gas system’s integrity.
Analysing pressure test results demands expertise. Professionals focus on key indicators such as:
Our team is adept at accurately analysing pressure readings throughout the test. We can swiftly diagnose problems and locate any leaks by observing pressure changes. A gas line that sustains consistent pressure testifies to a properly installed and sound system.
At Seven Hills Plumbing, we adhere to strict standards when determining if a gas line has passed pressure testing. Our priority is keeping homes and businesses safe by identifying any leaks or weaknesses before gas supply commences.
A timely and correct response is imperative when a gas leak is uncovered during pressure testing to mitigate risks and resolve the issue.
As soon as the pressure gauge indicates a drop, the first step is to immediately stop the test and vent the pressurised gas from the line safely. The area should be well-ventilated and any ignition sources removed.
The leak location can be identified by applying leak detection solution to joints and connections and looking for bubbles, ensuring there no misleading readings. All leaks must be repaired, no matter how small.
Regarding gas line integrity, repairs should be permanent and the line must undergo re-pressurisation and re-testing to ensure it’s leak-free before approval for use.
It is essential to make sure gas leaks are corrected before the line is connected to the gas supply and put into service. Never ignore leaks or use temporary fixes. Our gas plumbers respond quickly if a leak appears during testing to rectify it to the highest safety standards.
At Seven Hills Plumbing, we understand the risks posed by gas leaks and take professional leak response seriously. Let our gas fitters inspect and pressure test your system to give you peace of mind about its integrity.
To carry out an effective gas line pressure test, proper planning and strict adherence to safety protocols are necessary. Below are some professional tips from Seven Hills Plumbing to guarantee a successful outcome:
Seasoned expertise is essential for conducting pressure tests on gas lines. Get professional assistance by contacting Seven Hills Plumbing at 1300 349 338 or visit our website.
Blocked drains can be prevented by using drain strainers, avoiding pouring oils down drains, clearing hair from drains, and more tips from Seven Hills Plumbing.
Read MoreNoticing signs of a household blocked drain like slow drainage, gurgling sounds, foul odours or overflowing water indicates you need an emergency plumber. Call Seven Hills Plumbing to dispatch a plumber to clear your blocked pipes before further damage.
Read MoreRestaurants and cafes frequently deal with blocked kitchen drains due to grease, fat and food buildup. Prevent clogged pipes through scraping plates, using drain strainers and avoiding pouring fats/oils down sinks. Or call a professional plumber to hydro jet pipes and permanently clear blockages.
Read MoreSeven Hills, 2147 NSW
We will call back as soon as possible.